Turning solutions
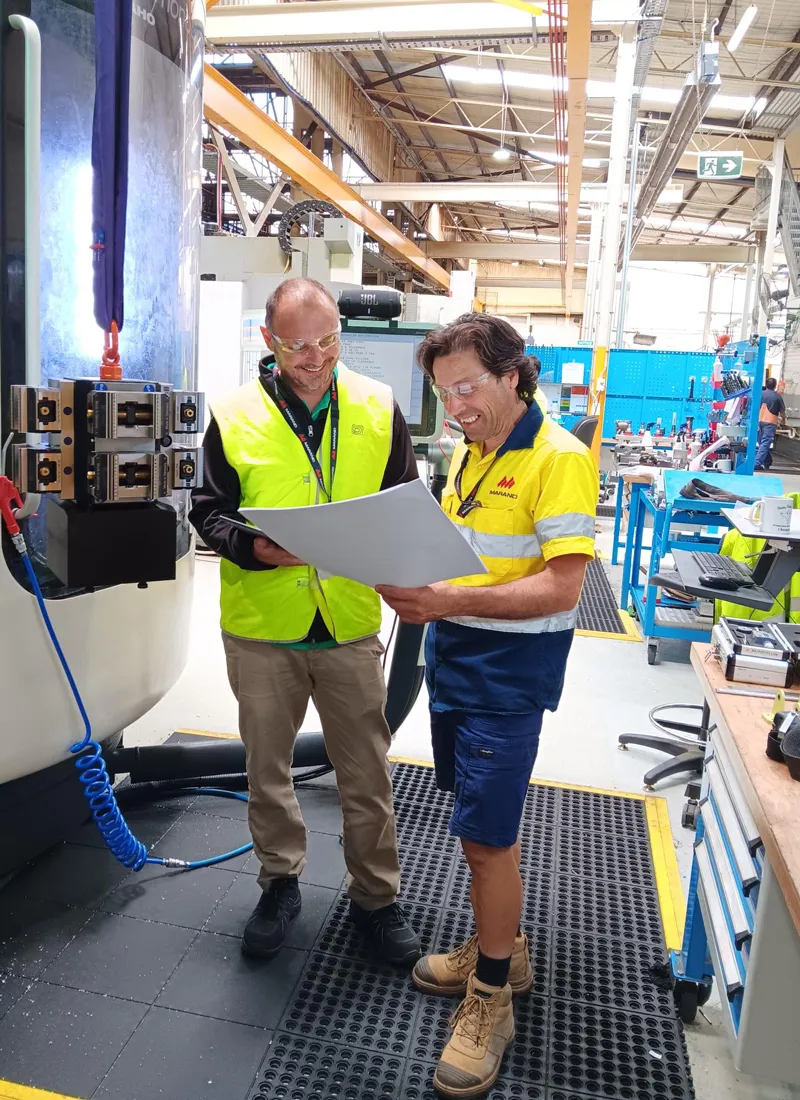
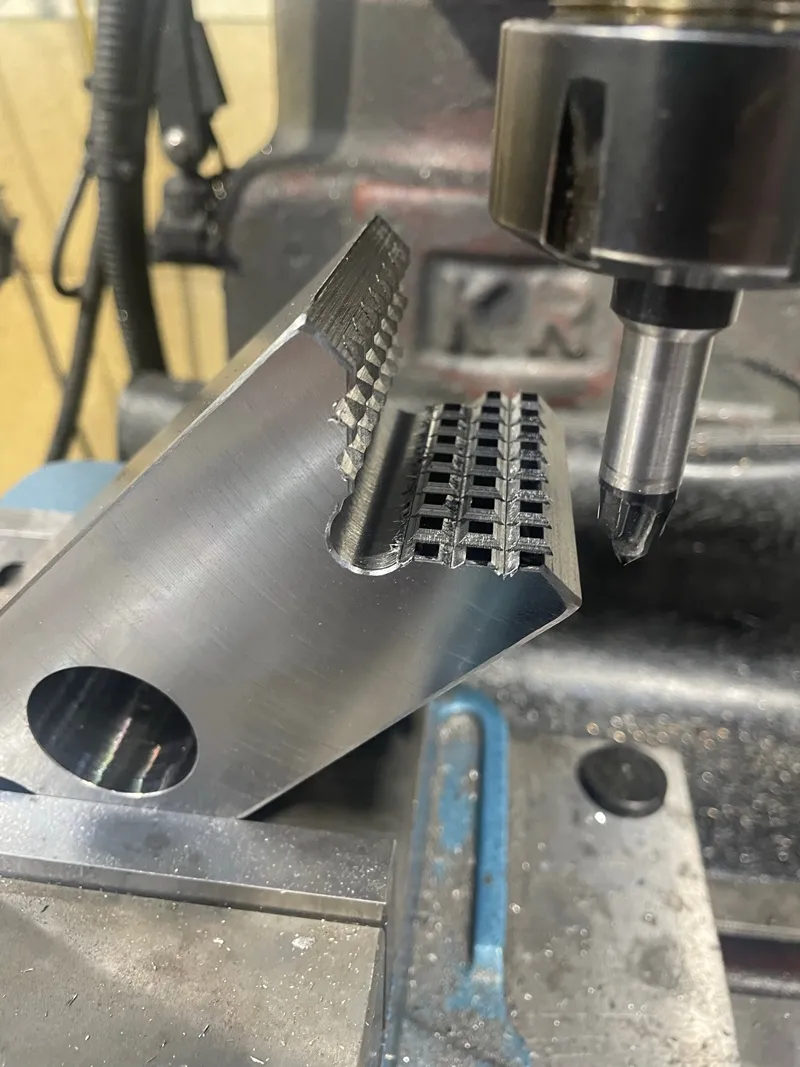
Global Innovation, local expertise in workholding solutions
We partner with leading global manufacturers to bring you high-performance CNC turning solutions that improve efficiency and reduce setup times while adapting to your machining needs. Our products streamline changeovers, lighten workloads, and ensure more productive workflows to keep you flexible and competitive.
Trusted brands, quality solutions

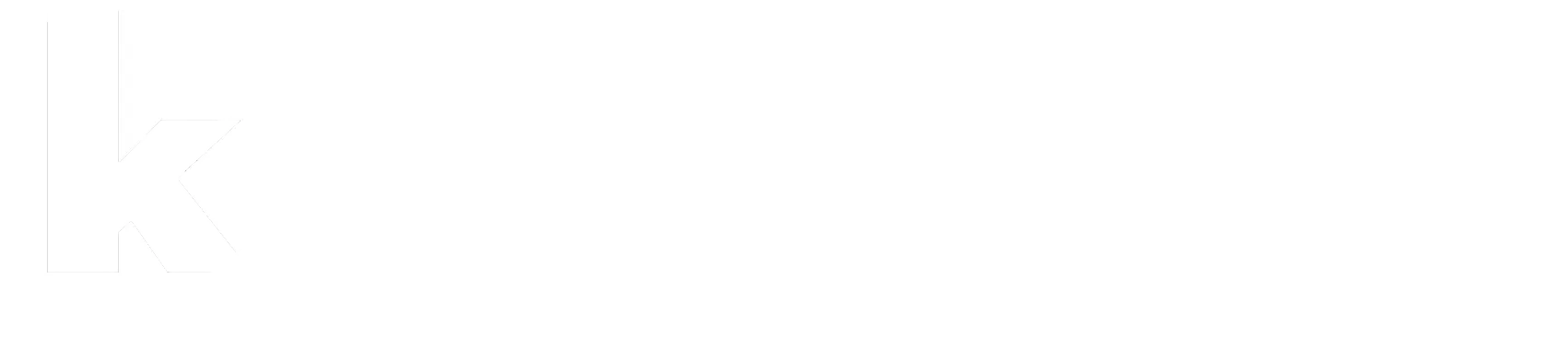
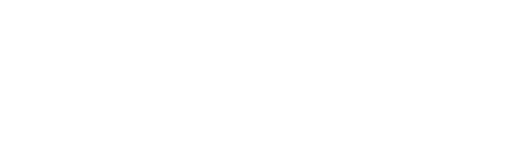
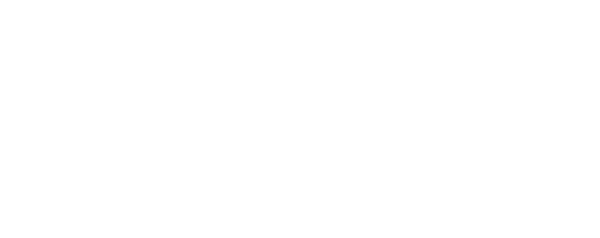
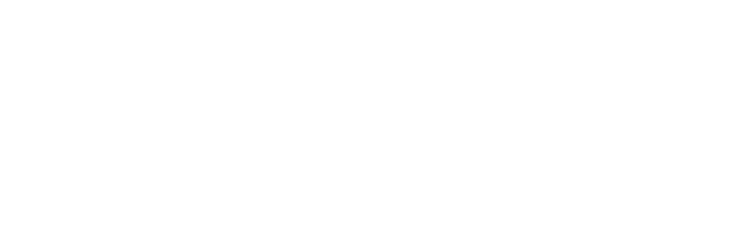
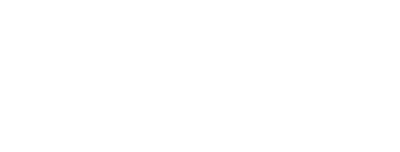
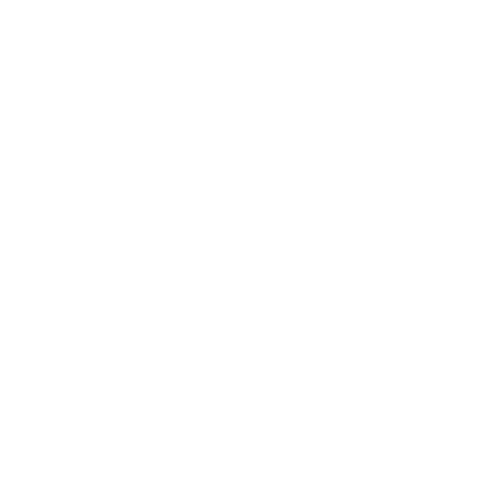

The Dimac advantage
Smart features, real benefits
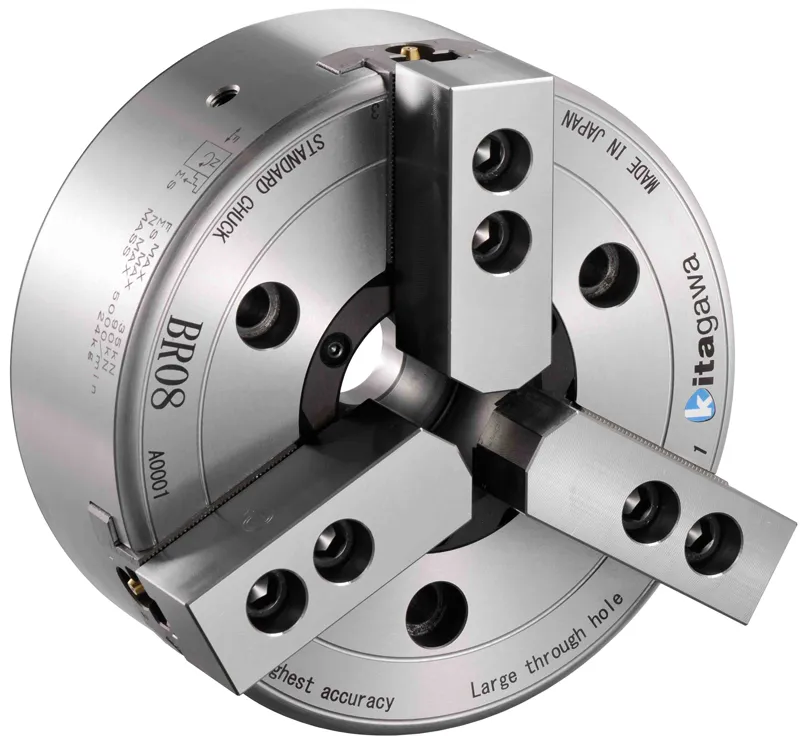
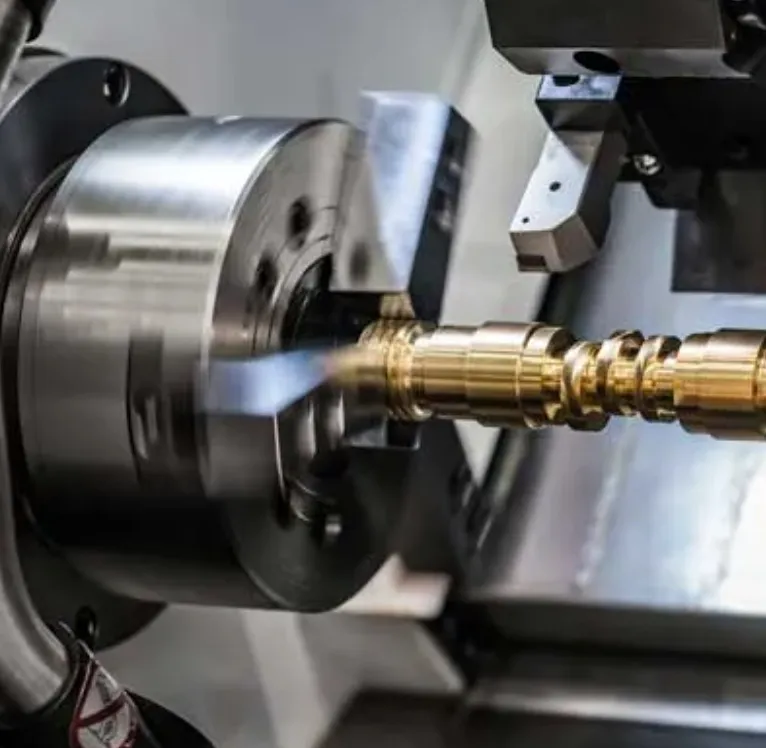
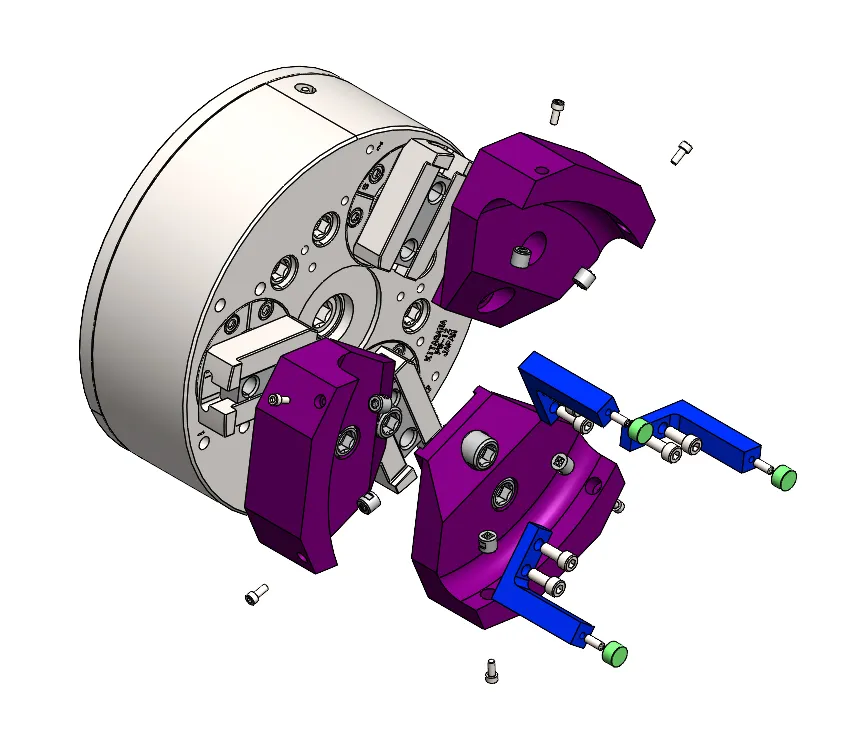
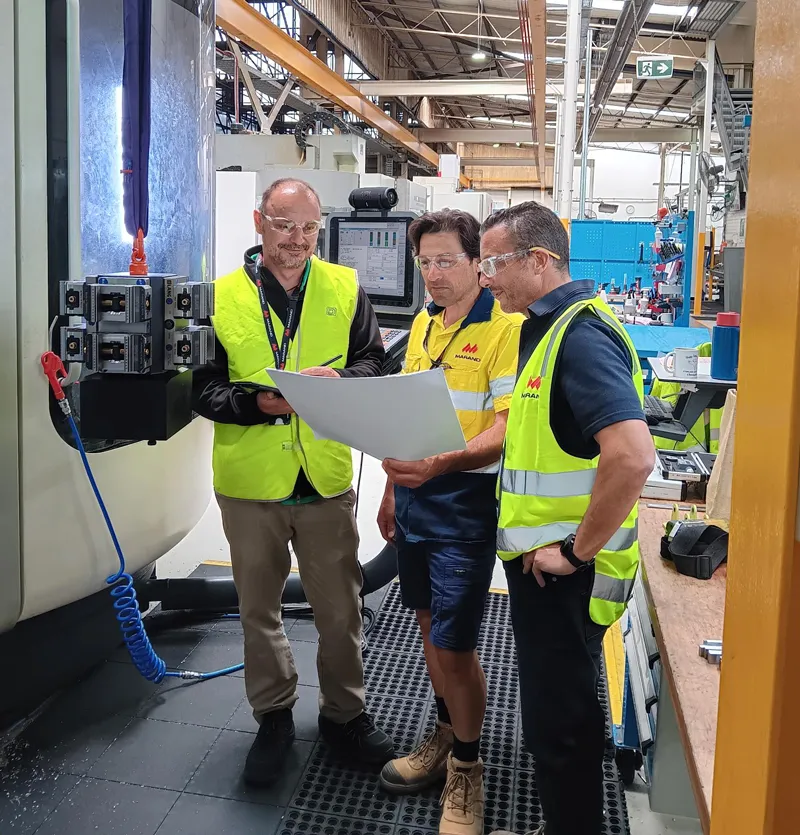
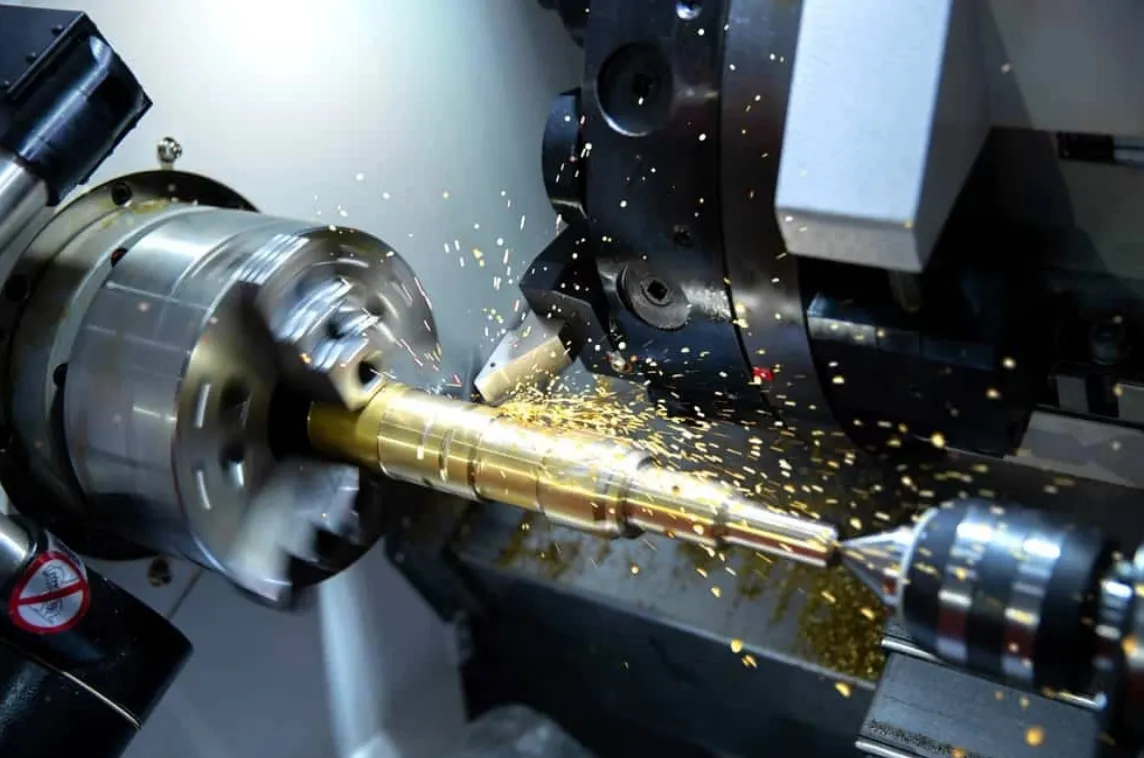
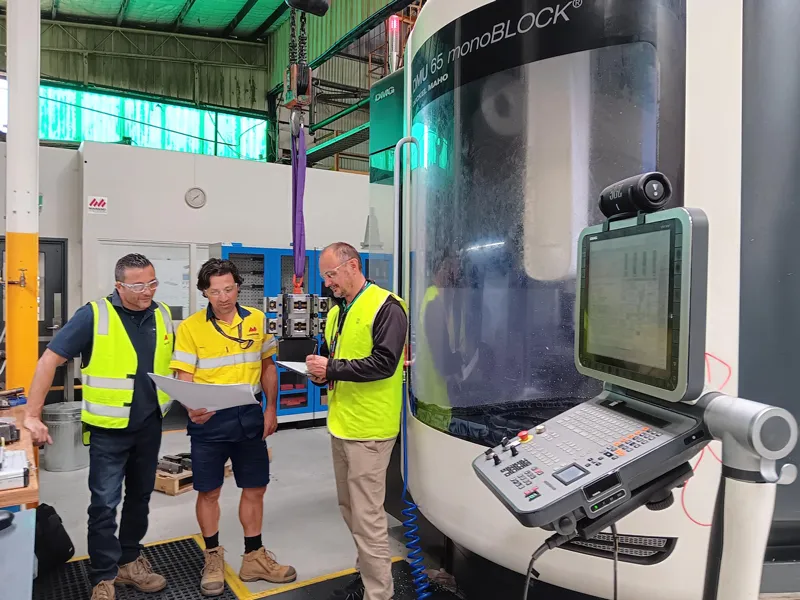
Let's discuss your CNC machine tool needs
Why work with us
Reliable, honest service backed by experience
Innovative CNC optimisation solutions
Commitment to sustainable manufacturing
Unmatched customer care and support
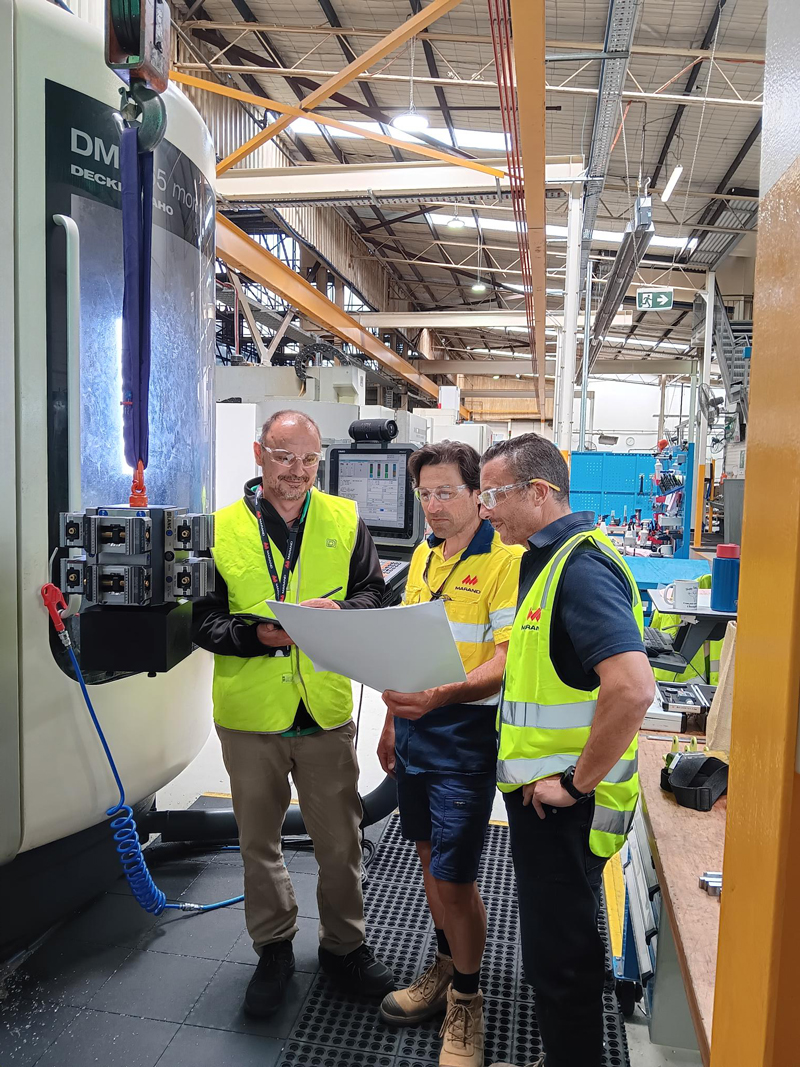
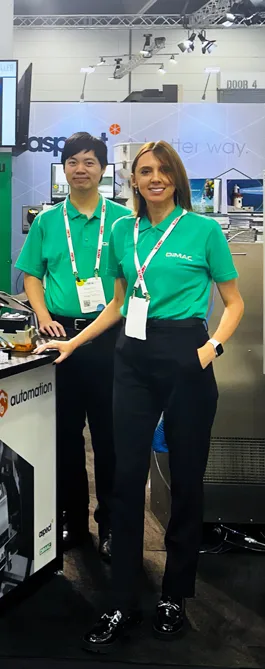
How can we help you?
Here, you'll find answers to common questions - but if you need more information or have a specific query, please feel free to reach out.
Chucks wear out over time, even with proper maintenance.
Watch for these signs:
- Higher hydraulic pressure needed to maintain a secure grip.
- Jaw flaring or kicking out when clamping a workpiece.
- Loss of concentricity, even with pre-machined soft jaws.
- Persistent chatter on the workpiece.
- Worn or damaged master jaw serrations.
If you notice any of these, it’s time to service or replace your chuck to keep machining safe and accurate.
Greasing your chuck with the right lubricant, like Kitagawa Chuck Grease Pro White, keeps it performing at its best. Proper lubrication reduces friction, increases grip force by 40–70%, and extends the chuck’s life. This grease resists extreme pressure, coolant washout, and centrifugal forces. Regular greasing ensures a consistent grip, reduces wear, and improves machining efficiency while cutting down maintenance and downtime.
We recommend applying two shots of grease per master jaw at the start of each shift. The amount may vary depending on grip cycles, grip force, materials, and operating conditions. Regular greasing reduces friction, keeps maximum grip force, and improves chuck efficiency while extending its life. Always use the manufacturer-recommended lubricant for the best results.
Yes, we sell master jaws. However, we would recommend replacing the chuck if the master jaws have been damaged, worn or involved in a crash as this can affect your chuck's performance and accuracy. If unsure our team is happy to help with expert advice.